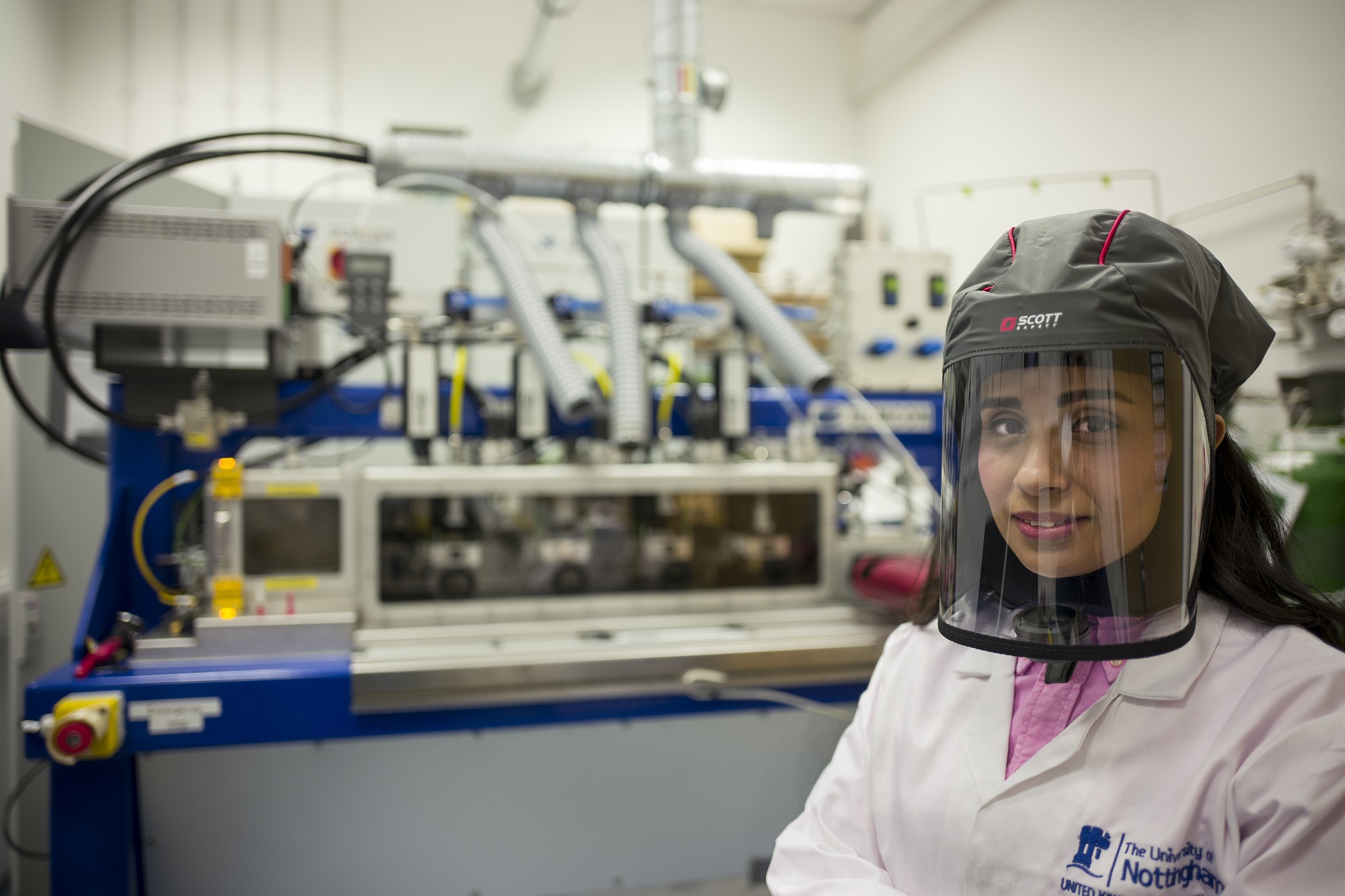
October 4, 2017, by Rob Ounsworth
Research Fellow Nesma: For me, this is the best place in the world to be
The University of Nottingham’s Anne McLaren Fellowships are aimed at outstanding female scholars in science, technology, engineering and medicine at the early stage of their academic careers. Nesma Aboulkhair is an Anne McLaren Research Fellow in the University of Nottingham’s Centre for Additive Manufacturing, where she researches the innovative 3D printing technology Metaljet, using the only machine of its kind in the world.
Why did you apply for a Fellowship?
A fellowship promotes independence, allowing you to research your passion. I pursued a career in research and academia mainly for the freedom of thought that it offers… we push the boundaries of knowledge. I believe that a fellowship is the most logical way to be able to do the work without the limitations of having an industrial sponsor to fund the research. It’s an honour in itself to hold a fellowship that promotes women in STEM fields. The fellowship considers the hurdles that we women face – there is still room for improvement to push women to achieve their goals in these fields.
Why Nottingham?
After finishing my PhD at Nottingham, I was advised to change university for the benefits of mobility. But I wasn’t convinced that I should leave one of the largest additive manufacturing groups in the world. The diversity in this group means that there will always be new stuff to learn. Therefore, I chose Nottingham. Only a couple of months after starting my postdoc, Professor Chris Tuck (my line manager) started talking to me about my career plans and how I should crack on right away to plan ahead. He and my mentor, Professor Richard Hague, motivated me to apply for fellowships and seek independence, making me even more confident that I made the right decision to stay at Nottingham. My mentors are not just interested in me spending hours in the lab to generate data so they can have publications – they really care about developing high-quality researchers. Last, but not least, this research group’s focus on the next generation of additive manufacturing sets us apart. I cannot find anything that would be more convincing to stay at Nottingham than this reason.
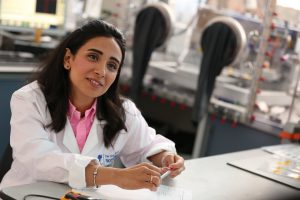
Nesma Aboulkhair in the Centre for Additive Manufacturing: “Nottingham has all what a researcher needs in terms of facilities and experiences to conduct high-quality research to impact the world.”
What has the experience been like?
The application process took seven-to-eight months. These were not the most relaxing months of my life but in retrospect I did enjoy every bit of it. If you are passionate about the research you want to conduct, you will find joy in the process of telling people about what you aspire to do and convincing them that it is worthy of funding and their trust. My love for my project grew with every day of the application process. Most importantly, the experience helped me learn how to put my research into context for the wider community.
How would you explain your research?
Metaljet is a highly novel droplet-on-demand technology. It dispenses molten micro-droplets of high temperature metals to produce 3D-printed micro-electronic components. My research tailors the process to produce a consistent stream of uniform molten copper droplets (melting point of 1085º C) to fabricate high-quality parts additively, which will be a world-first. Processing of copper via additive techniques is problematic and this investigation will be highly novel. The research will also look into the deposition of the droplets onto an insulating substrate to ensure a good sound bond. Furthermore, it will study the stacking of the droplets to construct defect-free parts. Metaljet is still a developmental process requiring fundamental research to optimise the process for defect-free parts. As with most metal additive manufacturing techniques, a part is built through creating lines that overlap to form a layer. This will allow higher degrees of complexity and flexibility in manufacturing intricate structures whilst maintaining accuracy and precision.
What inspired you to pursue this area?
I am a mechanical engineer, specialising in materials and manufacturing, so this fits perfectly within the expertise that I have gathered during my studies and working in the industry. Technological devices are becoming ever-more compact and complex, with ever-increasing demands for functionality and efficiency. This demands an exponential increase in the pace of development of manufacturing technologies. I wanted to contribute to this by helping present the manufacturers with a novel metal 3D-printer to be used for manufacturing 3D electronics. This will save resources, reduce production costs and end-products’ prices.
How will your research affect the average person?
Micro-electronic components manufacturers will have unprecedented ability to fabricate complex and intricate structures. They will be able to produce more efficient components for the technological products that are used every day to make lives easier and more productive. For example, this project will promote the possibility of fabricating 3D electronics that will reduce packaging and energy consumption in addition to increasing robustness. This process uses only the material needed to produce the part so it saves on raw materials and lowers costs and so is much less damaging to the environment. We are bridging the gap between the technology and the end-user manufacturers.
What challenges are you hoping to tackle?
Metaljet is a bespoke machine so there is no experience out there with running the system and it requires troubleshooting. We now have a significantly stable system – but of course, we’re always alert for any Metaljet surprises! Scientifically, for example, I would like to print the copper droplets on to a dielectric substrate to be used in electronic applications. There is a chance that I might not be able to find a dielectric substrate that would be compatible with copper, meaning that I will not be able to get my droplets to stick to the substrate. But again, I believe my planned solutions have strong potential to mitigate these risks. As I have learnt at Nottingham, achieving a novel solution should always be my aim.
What has been the greatest moment of your career so far?
This is a hard one. I am still in a very early career stage but, so far, my career path has been full of great moments. For me, the greatest moment so far was holding the first 3D printed object produced by Metaljet drop-by-drop from a high temperature metal, and knowing that it was the first in the world.
Who or what has helped you get to where you are today?
First and foremost, my family. They had faith in us and so we had all the confidence we needed to succeed. I am also indebted to the invaluable education that I have received at Cairo University and The American University in Cairo (Egypt), and The University of Nottingham. The bright academics at these institutions armed me with the knowledge I needed to be where I am today.
What advice would you give to someone starting out?
Only do what you are passionate about and don’t try to convince yourself if the passion isn’t there. Research is a tough field – we are pushing the boundaries of knowledge and a research problem lives with you day and night. You think about it when you are out and about, in your sleep (believe me, it happens), just all the time. How can you spend as much time with something you are not deeply passionate about!
How does being based at the University of Nottingham allow you to fulfil your research aspirations?
Well, Nottingham has all what a researcher needs in terms of facilities and experiences to conduct high-quality research to impact the world. My research is based on an additive manufacturing technology available only at Nottingham, where the University is internationally leading. It fits within The University’s Transformative Technologies Global Research Theme, and will contribute to the objective of the Advanced Manufacturing Research Priority Area to become a world-leading hub for innovation in advanced manufacturing. The University is investing in the infrastructure of my area of research as demonstrated by the newly established Institute of Advanced Manufacturing, where the Centre for Additive Manufacturing plays a vital role. Furthermore, the recently launched Nanoscale and Microscale Research Centre (NMRC) has the state-of-the-art equipment that will help me conduct high-class research to be published in prestigious journals.
No comments yet, fill out a comment to be the first
Leave a Reply