
September 6, 2017, by Shirlene Campbell Ritchie
TexGen: Weaving the way forward
Drs Louise Brown, Senior Research Fellow and Uresha Patel, a Postdoctoral Research Associate, discuss how TexGen, a textile geometry modelling software program developed by the University of Nottingham, is fast becoming a geometric pre-processor of choice in a wide range of industries.
TexGen is a tool which is used for generating realistic geometric representations of textiles including 2D and complex 3D structures. The software was first developed by Drs François Robitaille, who held a postdoctoral position in the Composites Group in the Department of Mechanical, Materials and Manufacturing Engineering in 1997 and Ben Souter, who was doing his PhD in Mechanical Engineering between 1998 and 2002. The software underwent a series of improvements over time.
In 2006, Dr Martin Sherburn a doctoral student who worked under the supervision of Prof Andy Long, Pro-Vice-Chancellor, Faculty of Engineering, developed Version 3 of the software and went on to release it as an open source program licensed under the General Public License. Since then, TexGen has been actively developed and it has now been downloaded over 30,000 times in 112 different countries.
Prof Long has been the driving force behind TexGen’s development. In addition to supervising many researchers who have been involved with developing the software, he has also been an investigator on various projects which have funded TexGen. These include acting as principal investigator on the Platform Grant for Textile Composites from 2009 to 2013 and the Engineering and Physical Sciences Research Council (EPSRC) Centre for Innovative Manufacturing in Composites from 2011 to 2016 – both of which have supported researchers who worked on developing TexGen. Prof Long is now the principal investigator for the EPSRC Future Composites Manufacturing Hub and his appointment will run from 2017 to 2023. This will see him continue to support TexGen and the research which uses it.
How it works
The software uses a kinematic modelling approach, which is based on the definition of yarn centrelines with cross-sections specified along the yarn length. Textiles are characterised using microscopy or x-ray micro-computed tomography images and geometric features are identified, which are then built into TexGen. In this way, models can be generated quickly and users need not have prior knowledge of the mechanical properties of the materials.
TexGen was initially developed to study composite materials which have gained prominence in line with the rising demand for lightweight, high strength materials. These include organic matrix composites, ceramic matrix composites and carbon fibre reinforced polymers, as well as honeycomb-like textile structures such as aramid materials, which are primarily used in body armour. Organic matrix composites have been used in the design and material selection phase for components used in fan and compressor systems, while ceramic matrix composites are commonly developed for compressor and turbine systems.
Textile composites are commonly produced either by layering 2D weaves to the required thickness or by creating complex 3D weaves which provide enhanced properties. By using TexGen to carry out ‘virtual tests’ on these materials, users have seen significant savings in costs and associated reductions in materials and time. This in turn, has enabled them to test a large number of patterns and narrow down the amount of composite materials that go forward to manufacture, further testing and trials.
As the global demand for textiles and textile composite materials continues to grow, TexGen enables its users to refine their materials selection processes. It offers a non-destructive method for the investigation of material properties and allows evaluation of interactions on the weave scale which would not be otherwise possible.
A stronger future
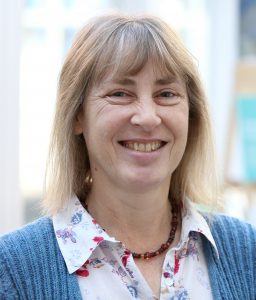
Dr Louise Brown, Senior Research Fellow, has been awarded the prestigious EPSRC Research Software Engineering Fellowship.
Dr Louise Brown, Senior Research Fellow, has been awarded the prestigious EPSRC Research Software Engineering Fellowship for her work in textile modelling and simulation using TexGen. In addition to improvements, TexGen will see the development of new features to meet the modelling requirements for the increasingly complex textiles and preforms which are used in composite materials. The Fellowship will help to widen the reach of the software beyond composites and identify new and emerging areas in textile technology which will require modelling and simulation capability.
For further information, please contact Dr Louise Brown on 0115 951 3979 or louise.brown@nottingham.ac.uk
No comments yet, fill out a comment to be the first
Leave a Reply