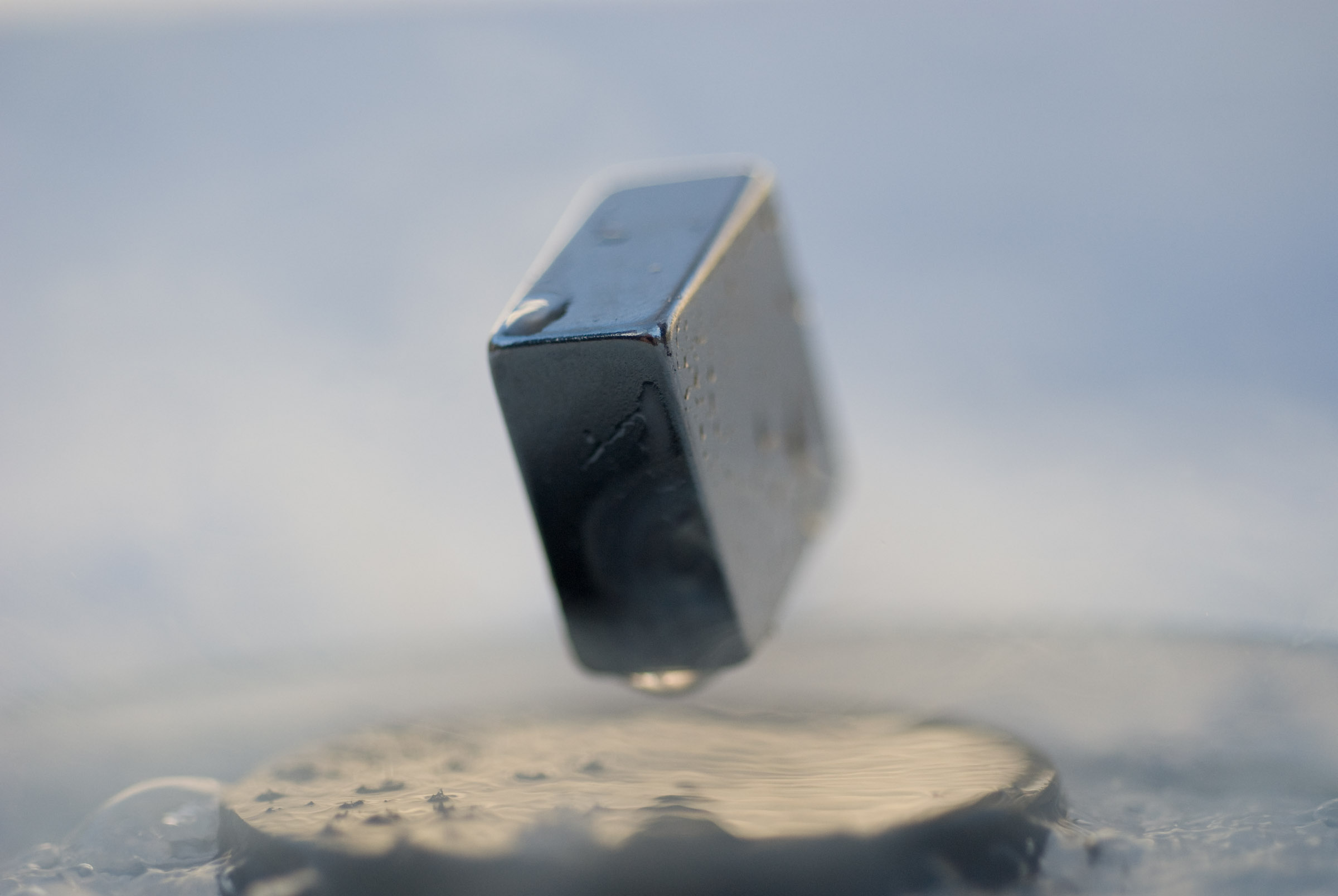
December 18, 2015, by Luca Bertola
Cryogenic applications for visionary aircraft concepts
The ambitious long-term environmental targets set by the European Commission (2011) and the Advisory Council for Aeronautics Research in Europe (ACARE) require airframers and their suppliers to improve the integration between an aircraft’s propulsion system and the airframe…
In particular, concepts such as the distribution of the thrust generation along an airframe’s main components and of ‘ingesting’ the fuselage boundary layer are considered to be of great importance in the industry’s attempts to fulfill ACARE requirements. However, for large aircraft the power densities are so large that they would require much higher power density subsystems than can be designed with current conventional technology.
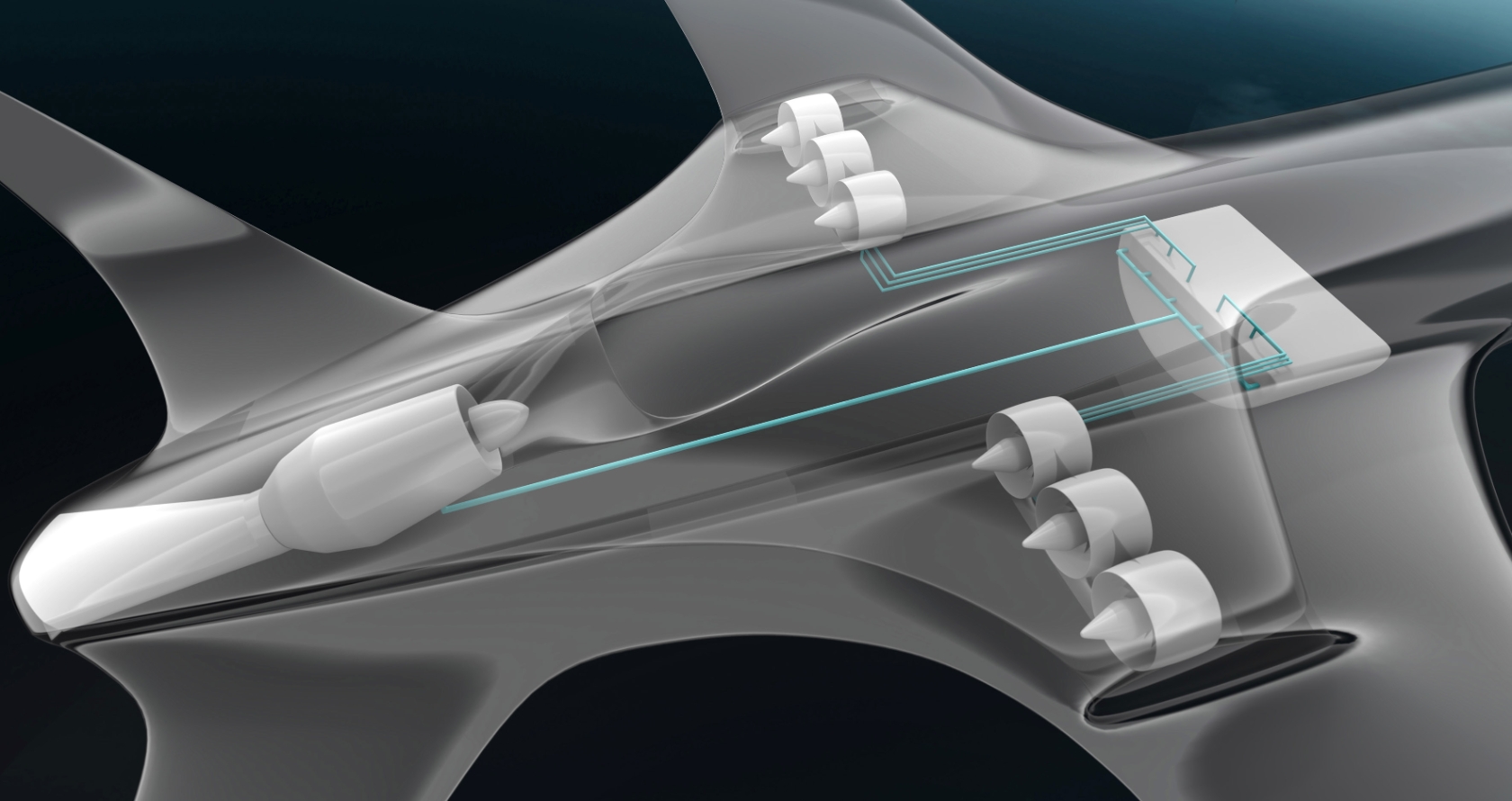
The E-Thrust is an electrical distributed propulsion system concept for lower fuel consumption, fewer emissions and less noise (Source: Airbus Group, 2016)
The international research community has therefore suggested that the electric machines within an aircraft may need ‘superconducting’ motors. A hybrid system could be the best solution, with modified gas-turbine alternators providing electric power to a large number of superconducting propulsors.
Numerous researchers today have proposed superconducting machines connected by a network with superconducting cables that will still require conventional power conversion, switches and protection device. However, a distributed propulsion aircraft would significantly gain in performance implementing fully superconducting power systems (reduced heat losses and no transitions between environmental and cryogenic temperature).
Cryogenic systems
While the international research has so far been largely focused on the electrical aspects of the superconducting system, less consideration has been given to the cryogenic system to support the high power superconductors. In general a cryogenic system is formed by a cooling system (also called cryocooler) that operates below the boiling temperature of the liquid nitrogen (77 K), a coolant that could be gaseous or liquid and an insulation system that limits the heat losses.
To maintain a closed loop of cold fluid at the superconductors’ operating temperature, fully centralized large cryocoolers have been identified to be likely the best option for aerospace applications for their low weight and high efficiency. Reciprocating cryocoolers are likely to be unsuitable for applications with large cooling power required. Their performances rely on regenerative materials which are bulky and heavy. Moreover, the reciprocal operations require regular maintenance and the deterioration of regenerative materials needs periodical substitutions. Scalability and reliability are crucial factors for the main cryocooler and indications are that Reverse-Brayton Cycle (RBC) would be the best suited. The cryogenic temperature the cryocooler has to maintain is related to the transition temperature of the superconducting material employed in the system.
Superconducting materials
Since the discovery of superconductivity, great efforts have been devoted to the discovery of materials with higher and higher transition temperatures. Indeed, the consistent amount of energy required to cool down large device at the temperature of Kelvin would discourage any practical applications. At present, the superconductor with highest transition temperature is a ceramic material compounded of mercury, barium, calcium, copper and oxygen which present no resistance under 138 K. Unfortunately, this superconducting material cannot be employed for engineering applications since it is too brittle to be used to produce cables. The high temperature superconducting wires that have been commercially available since 1990 are made from a powder of bismuth-strontium-calcium-copper-oxide (BSCCO) which is deposited to form a film or a tape.
Most recently, second generation high temperature superconducting wires have been manufactured in a similar way using yttrium-barium-copper-oxide (YBCO). This material is superconductive at 92 K, but it presents electromagnetic properties suitable for electrical machines at lower temperatures (typically at the nitrogen boiling temperature or below).
Low temperature superconductors
Even though high temperature superconductors are a promising technology for future applications, low temperature superconductors are vastly adopted worldwide for their structural and electromagnetic properties. In particular, recent progress in a new superconducting material Magnesium Diboride (MgB2), allows the design of superconducting electrical machines that are much more power dense than convectional machine at environmental temperature. MgB2 presents no resistance at 39 K, but it shows interesting electromagnetic properties between 20 and 30 K. The application of MgB2 at 20 K is particularly interesting from the thermodynamic point of view since it allows for the use of liquid hydrogen as main coolant and therefore the possibility to take advantage of its great capability of absorbing heat while it evaporates. The combination of MgB2 superconducting cables and electrical machines, cooled down by liquid hydrogen may represent a viable technology for the power distribution system and the thrust generation system of future aircraft.
Design constraints
The design of a cryocooler for aerospace applications that is able to maintain a temperature of 20 K, removing considerable amount of heat, is really challenging. The question of how to dispose of the waste heat in the superconducting system and the associated cryocooling system will have a major impact on the overall aircraft design and its eventual performance. Simple calculations show that using ambient air, even at high altitudes, as the final heat sink will lead to challenging design constraints, in particular due to the low thermal efficiency that can be achieved. A low temperature heat sink is required when operating at temperatures below 60 K.
The main options that could be considered are liquid methane (LCH4) or liquid natural gas, and liquid hydrogen (LH2), due to their high latent heat, their boiling points and their heating values. Their usefulness as a fuel is of particular interest because they can offset the kerosene carried by the aircraft to mitigate the additional mass required by the cryogenic system. It is noted that LCH4 in particular has excellent combustive qualities and has higher chemical energy content by mass than kerosene. Modifications to gas turbine engines in order to burn methane would be relatively minor. Using hydrogen as a fuel may be more complex, since it would require larger modifications to the engine design. A more likely use of spent hydrogen coolant may be in an auxiliary power unit (APU) to provide additional electrical power.
The mass of the cryocooler can be generally expressed as a function of the input power required by the cooling cycle and since the weight is a crucial parameter to optimize in aerospace applications, the inefficiency of the superconducting electrical machines would severely restrict the scope for a feasible system solution. The target efficiency to make superconducting distributed propulsion a viable solution for ACARE requirements is 99.7%.
Note about the author:
The author further investigated cryogenic and superconducting technologies during his secondment with Airbus Group Innovation as part of the Institute for Aerospace Technology’s INNOVATE project, as an opportunity to improve his professional skills in an industrial environment.
You present a very good article, I wait for the newest article. Happy to visit your site! Obat Sakit Pinggang Sebelah Kanan