January 8, 2015, by Andrea Bristot
Aero engine efficiency: how far can we really get?
Current aero engine manufacturers are feeling increasing pressure from customers and public institutions to reduce fuel consumption. The need of airline companies to minimise operational costs, coupled with a general pressure to have “greener” engines (as clearly outlined in EU’s ACARE and US’s FAA targets), requires the aero engines industry to be one of the most advanced fields of research in engineering. High competition between the manufacturers pushes the limits of new technologies further to reduce fuel consumption, emissions, noise, and maintenance costs. But how further can we push the thermal cycle of a jet engine to increase the efficiency?
From the laws of thermodynamics, we know that to obtain useful work from a thermal machine we need to compress the working fluid (i.e. air in our case), heat it up and then convert the energy from the hot gases into mechanical and kinetic energy. In other words: suck, squeeze, burn, and blow.
How good we are in converting the thermal energy from the burning fuel/air mixture into useful energy will determine the efficiency of our machine. Our path now splits between what we could get out of the fuel and what we can actually obtain.
For the first point, once more, the laws of thermodynamics come in a simple form to help us. For the ideal Brayton cycle, underlying the working principle of the jet engines, we find that the thermal efficiency increases as we raise the pressure ratio between the combustion chamber and the outside atmosphere. The correlation is not linear, implying that the increase in pressure ratios will need to be progressively larger to make a further step in efficiency improvement.
If we drop some numbers into our equation, we find that for the current pressure ratio value of 50 achievable in the newest commercial engines, the ideal thermal efficiency (e.g. the ratio between net work output and heat input) is on the order of 67%. To reach the 70% threshold, we need to go up to a pressure ratio value of 68. Which means a 36% higher pressure ratio for a 3% increase in efficiency, and implies significant technical challenges.
Our challenge now moves to the second part of the path, which is the real efficiency of the engine. This parameter quantifies the actual work output of the machine against the heat input. Hence, in practical terms, it is more useful to understand how well the engine converts the available energy into usable work. Now many more parameters come into play.
First of all, the fuel burn of the engine during a flight will depend on how well we convert the gas energy into propulsion, which is quantified by the propulsive efficiency. The maximum propulsive efficiency is achieved when the exhaust gases have the same velocity of the surrounding air, which of course is an ideal condition. We can raise the propulsive efficiency by increasing the fan size, which is roughly the equivalent of equipping a scuba diver with longer fins: the mass flow going through the engine will be larger, but expelled at a lower speed.
The product between the real thermal efficiency and the propulsive efficiency gives our desired outcome, e.g. the overall engine efficiency, which translates into fuel burn rate. As the parameters affecting the overall efficiency are several, apposite programs have been developed to calculate its value. One simple, useful tool to quantify the impact of the different parameters on the jet engine efficiency is provided by NASA and is available here.
A trial made with this tool, using up-to-date input values, gave an overall efficiency of about 50% for an aircraft at cruise. This result is good, but quite far from the 67% we would ideally have. Where has the remaining energy gone?
Part of it, as explained above, is missing due to the propulsive efficiency being less than ideal. Hence, it has been lost in the mixing of the gases expelled by the engine with the surrounding air, as a result of turbulent collisions between air particles.
The other big slice missing is due to the efficiency of the components inside the engine, which is not as ideal as we would like. Air is in fact difficult to compress; it tends to heat up and therefore dissipates part of the energy input as heat. The combustion itself leads to energy losses, and although almost 100% of the fuel is nowadays burnt, small portions of it can escape from the combustion chamber. Finally, the harsh conditions in the turbine lead to the need for cooling systems, which come at the cost of energy losses. Additionally, all the subsystems inside the engine such as gears, electrical systems, pneumatic systems and oil systems imply power off-takes.
With all of this in mind, we find three options to increase the overall engine efficiency:
- increase the ideal thermal efficiency, hence the upper limit that can be reached
- increase the propulsive efficiency
- bring the real thermal efficiency closer to the ideal value
For the first point, all we ideally need to do is to increase the engine overall pressure ratio (OPR). Although it may sound simple, the technical challenges involved are considerable: the more we compress the air, the higher its temperature is. This implies high heat dissipation, meaning increased energy losses in the compressor. Moreover, as the volume of air diminishes, the compressor blades will be progressively shorter, up to a point in which the gap between the blade and the walls becomes a significant part of the blade length, leading to unacceptable air backflows. To address these issues, novel architectures need to be established, to include intercoolers and low-diameter compressors.
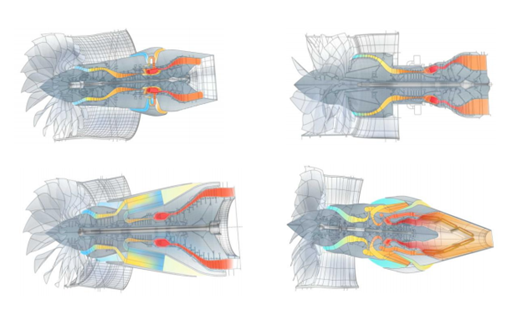
Figure 2 – Some high-OPR engine concepts. Source: NEWAC
To address our second point, e.g. the increase in propulsive efficiency, the current trend is to move towards larger fans, thus increasing their contribution to the overall propulsion. In this case, the challenge is to allow both the fan and the turbine driving it to rotate at their optimal speed.
The allowance for decoupling the rotational speeds was recently achieved by Pratt & Whitney, which developed in collaboration with Avio a fan-drive gear system capable of handling the torque delivered by the low pressure turbine, for its PurePower medium-range engine family. Given the feasibility and validity of this system, Rolls-Royce recently announced it will adopt as well a power gearbox in its UltraFan long-range engine concept.
The last of our three points is the improvement of the component efficiency, in order to bring the real thermal efficiency closer to its corresponding ideal value. This can be done through the improvement in the design of components such as the compressor, combustor, and turbine, a better thermal management of the engine core, innovative materials and a rationalisation of power off-takes. For the latter purpose, a trend towards more electric engine cores has been developed across the industry, with the aim of simplifying the engine architecture by removing, or at least downsizing, the pneumatic, hydraulic and mechanical off-takes. A significant slice of The University of Nottingham’s activities within its Power Electronics, Machines and Control Research Group) aim to explore and develop technologies for this purpose. Other projects aiming to improve the aero engine core efficiency are part of the Work Package 1 of the INNOVATE program. These projects address the development of technologies for improved oil systems and air sealing, while envisaging the integration of novel electrical machinery inside the core.
To conclude, aero engine industry faces significant ongoing challenges in order to develop more fuel-efficient engines. The upper bound of the energy efficiency limit is set by the laws of thermodynamics, which give us a precise value of how far we can get with our current engine cycle.
For the moment, investments look to be set towards the improvement of the engine components’ and subsystems’ efficiency, together with the improvement of propulsive efficiency. The margins for improvement in this sense are, although tight, still promising, and allow the aero engine architectures to evolve progressively, with few risky discontinuities from well-established, reliable baseline designs.
From a research point of view, however, all the concepts that could give significant leaps in terms of design and fuel efficiency are being investigated, so that in the far future, engine architectures may change significantly to allow for more complex, energy-efficient cycles including intercooling and regeneration.
[…] While progressive optimisation of the current aircraft is ongoing (aerodynamic improvements, engine efficiency, increased use of composite materials, etc.) other revolutionary concepts are being studied as […]