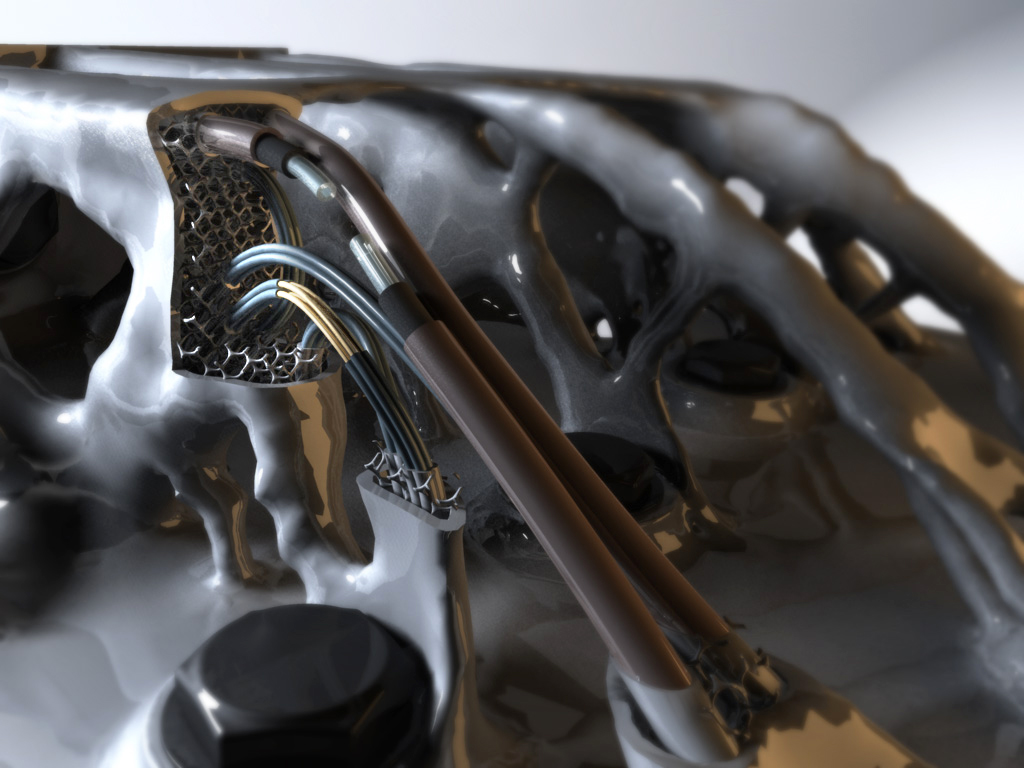
February 17, 2014, by Michele Garibaldi
3D Printing: Just another media hype?
With the Aerospace industry saying no, the future of this technology has never looked brighter
“Giving everyone the possibility to print whatever they want, wherever they are”. This seems to be the predominant ideologue that newspapers, online commentators and TV programmes popularise when discussing the virtues and possibilities associated with 3D printing. The potential for such flexibility, as promised in these utopian sound bites, has also drawn negative press in recent times, not least when the code required to print a fully-operational hand gun was posted to an online forum! However, the real benefit for this area of manufacturing technology, which has grabbed so many headlines in recent months, may be seen as less “cool”, but much more valuable than the ability to print what you want, when you want.The real breakthrough should come with the ability to 3D print metallic parts for industrial production, as opposed to today’s prototyping items. That is the goal that researchers in Additive Manufacturing (AM), the branch of 3D printing applied to the manufacturing industry, hope to achieve in the not-too-distant future.
At the end of last year, Impact (The University of Nottingham’s Student Magazine), wrote an article dedicated to 3D printing. The piece nicely outlined what AM actually entails:
“Mass production is always going to be cheaper […] when it comes to making thousands of identical objects. However, 3D Printing is incredibly useful for making unique objects which need a very specific shape, some of which cannot be made by regular manufacturing techniques”.
Add to this the possibilities provided by AM with regards to freedom in design for the production of weight-saving metal components and it is not difficult to see why the industry sector that is taking AM most seriously is that of aerospace. One of the most prominent corporate names regularly associated with AM in the press is General Electric (GE) Aviation, the world’s biggest manufacturer of aero-engines. GE is leading the way with its plans to produce a fuel nozzle using Selective Laser Melting (SLM). And last summer it was again GE who promoted an online challenge for the design of a Titanium alloy engine bracket to be fabricated using AM.
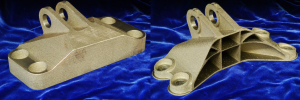
For the GE bracket challenge, almost 700 designs were proposed. On the left of this figure, the 2,033 g bracket GE asked the community to improve upon. On the right, the winning design, which slashed the weight to 327 g. Images taken from https://grabcad.com/challenges/ge-jet-engine-bracket-challenge/results
The interest within the aerospace sector in AM does not end there. Just a few weeks ago Arcam, a Sweden-based producer of machines for the 3D printing of metal components, publicly announced that a major aerospace industry client (still secret) ordered a number of electron beam melting (EBM) systems. And it’s not just the private sector. The decision of the UK Chancellor, George Osborne, to invest up to £60million in AM as part of the government’s £2 billion aerospace strategy is another sign of the rising awareness of the potential of this technology.
The road to scalability may still be long, given the poor capability of current printers to guarantee repeatability. In this respect, a greater willingness on the part of the printer producers to innovate would help (for example, the concept of closed loop control has not yet been introduced in laser- and electron beam-based machines).
However, the eagerness of both the private and public sectors to invest heavily in AM makes us hope that a controlled environment will come to represent the development of AM as an industrial practice, which in turn will replace the hype in the media with real achievement.
Loved the GE weight reduction example!
It is surely one of the most impressive examples showing the advantages of AM over classical manufacturing. But the best has yet to come!